Burrs: the most important principles
Burrs from PFERD TOOLS stand for quality, variety and reliability
The world of burrs is multifaceted, challenging and highly professional. In this practical guide, PFERD TOOLS outlines the basic principles of this group of tools. Become a PFERD TOOLS product specialist step by step.
Using burrs: working with geometrically defined cutting edges
In manufacturing, burrs can be used for all manner of machining processes. They can be used for chamfering, levelling, deburring, cutting out holes, for surface work, and for working on weld seams. Burrs are the very embodiment of a multi-purpose tool.
PFERD TOOLS range: the perfect tool for any application
PFERD TOOLS burrs fall into two basic categories: HSS rotary cutters and tungsten carbide burrs.
HSS rotary cutters have a special tooth geometry and have been manufactured to a high quality. They can be used cost-effectively with low-power tool drives in a low rotational speed range. The tooth cutting edges of these burrs are very stable, as they are made of high-speed steel (HSS).
Recommendations for use:
- Use HSS rotary cutters if your drive unit does not allow for high rotational speeds. In contrast to tungsten carbide burrs, HSS rotary cutters need to be used with lower rotational speeds.
- When used on soft materials, HSS rotary cutters can be an economical alternative to tungsten carbide burrs.
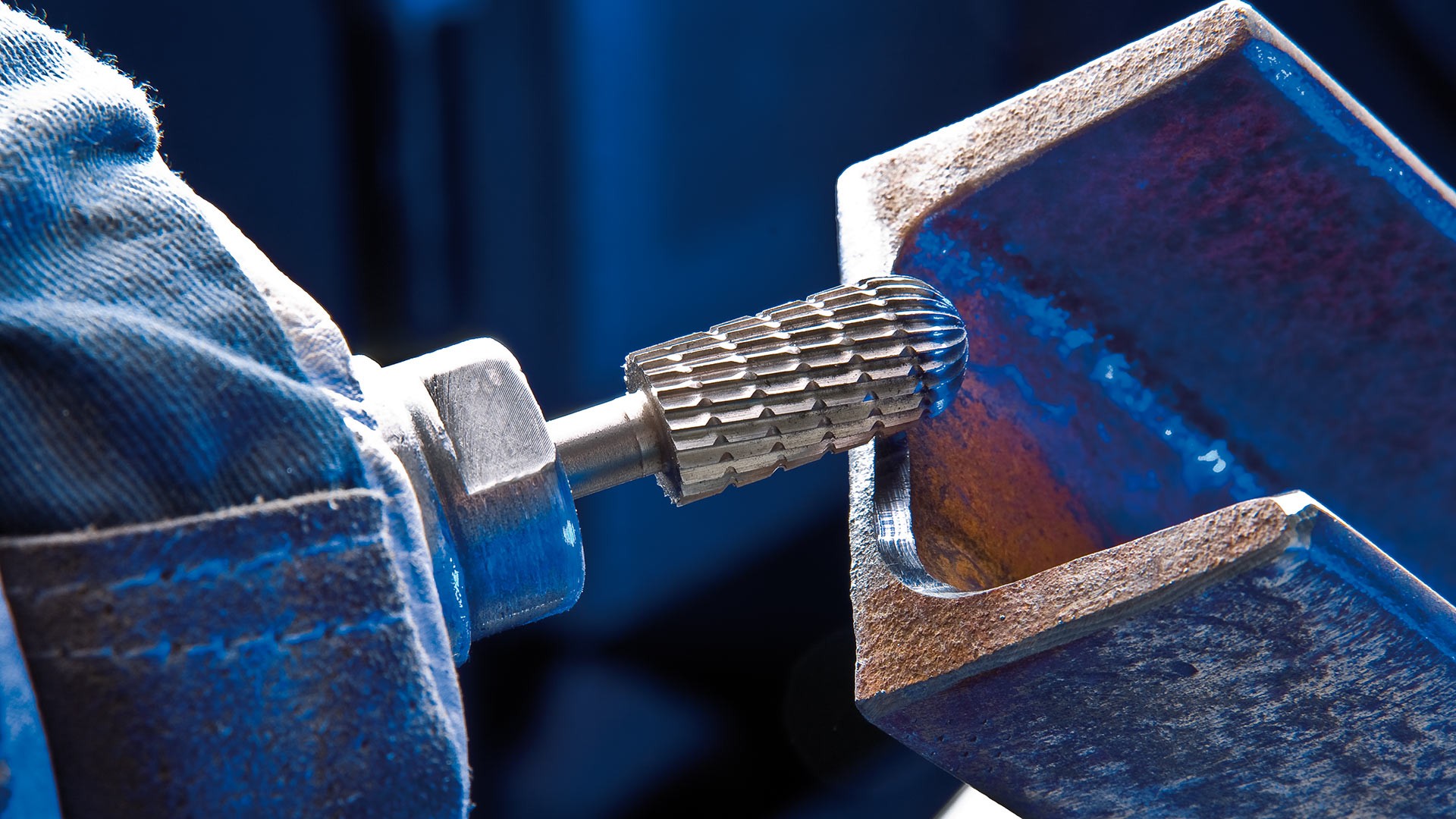
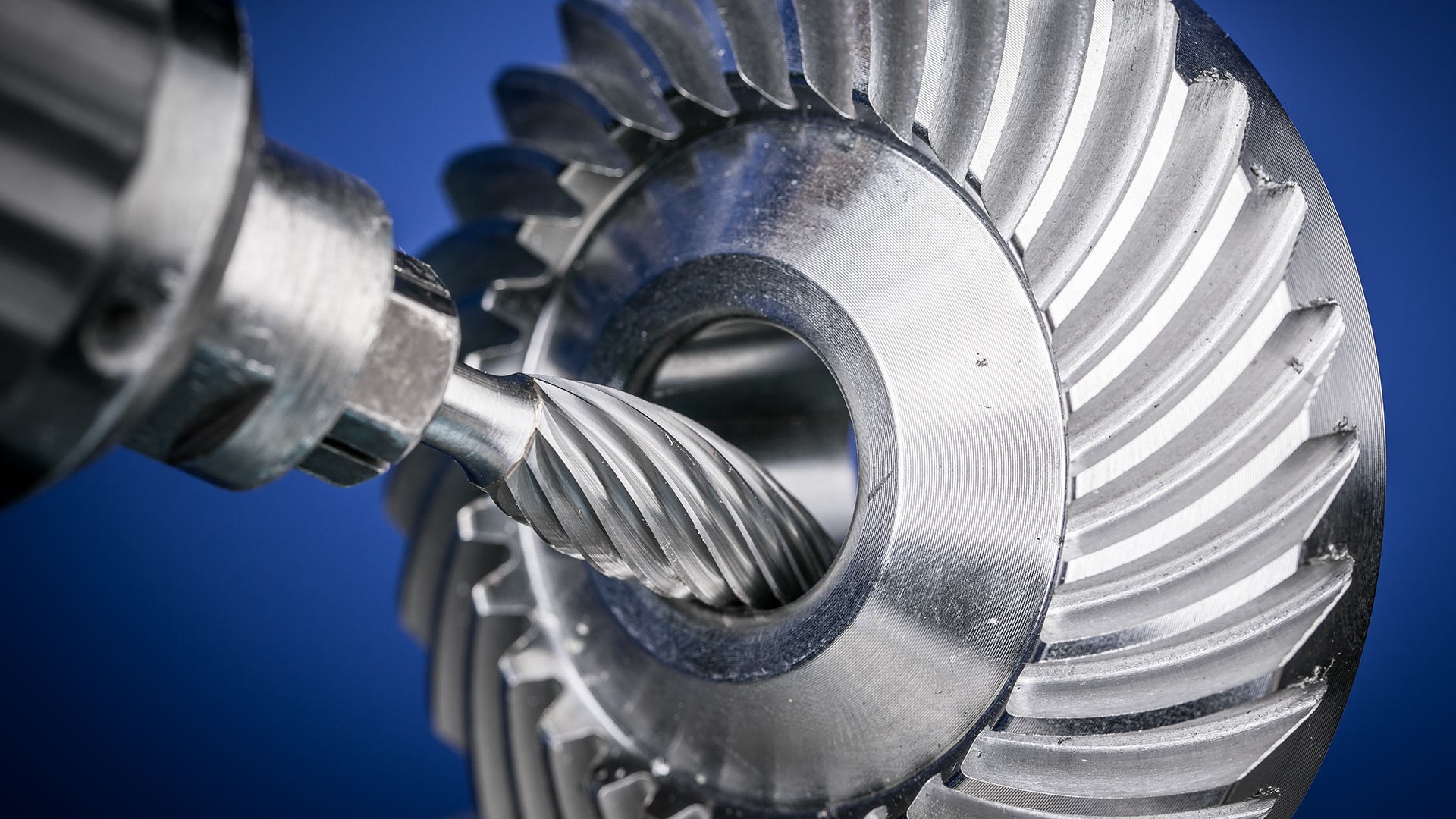
Users across all manner of industries often choose to use a burr that is made of tungsten carbide (TC). Tungsten carbide burrs are a more modern solution for chamfering, levelling, deburring and working on weld seems compared with HSS rotary cutters. They have a considerably higher stock removal rate and tool life than the HSS variant. TC burrs should be used with high-performance drives and, if possible, high rotational speeds within the recommended rotational speed ranges/average speed ranges.
Burr design: tungsten carbide burrs
PFERD TOOLS has various different types of tungsten carbide burrs in its extensive product range. Burrs have a very distinct shape and dimensions, and are further characterised by their cut area and shank. PFERD TOOLS offers TC burrs with numerous different cuts for general applications and high-performance applications, burrs with HICOAT coating, and long shank versions and special solutions.
Regardless of the specified criteria, burrs fall into two different categories: solid tungsten carbide burrs and tungsten carbide burrs with steel shank.
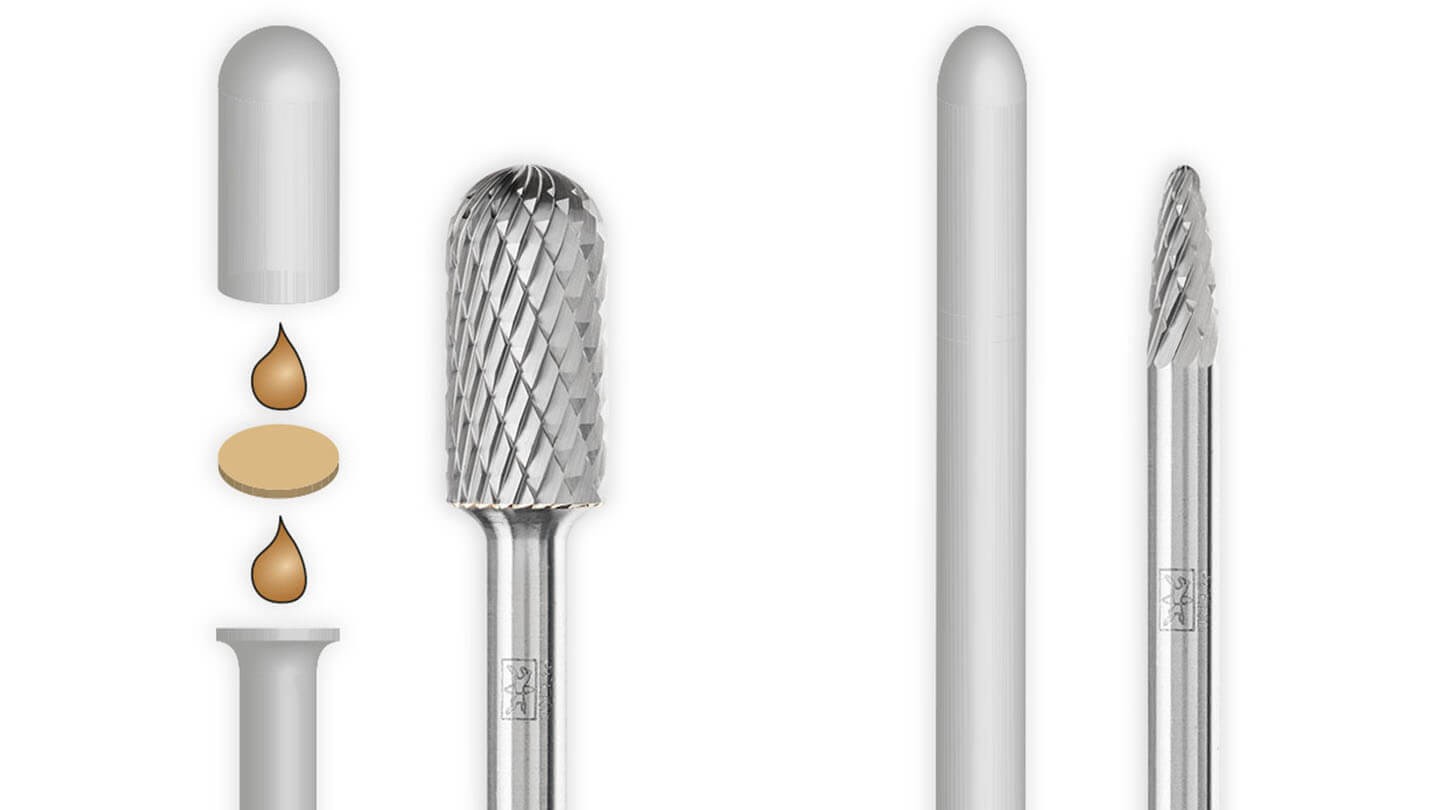
Solid tungsten carbide burrs are characterised by the fact that their cut area and the shank are made from a single piece. The blank piece is made from a tungsten carbide rod and profiled into the respective shape using a diamond grinding disc. Solid tungsten carbide burrs generally have a toothed area diameter that is smaller or equal to the diameter of the shank.
Burr dia. (d₁) ≤ shank dia.(d₂)
A characteristic of tungsten carbide burrs with a steel shaft is that only the cut area is made of tungsten carbide. Both components are joined together using a special soldering process before profiling the cut area. The diameter of the cut area is generally greater than that of the shank.
Burr dia. (d₁) > shank dia.(d₂)
PFERD TOOLS also offers these two different types of burrs as versions with a long shank. GL = gross (i.e. total) length (solid tungsten carbide), SL = shank length (long steel shank). Tungsten carbide burrs with a long shank can be shortened if required. Tungsten carbide burrs with the designation GL 75 mm are made from solid tungsten carbide, which means they can only be shortened using diamond tools.
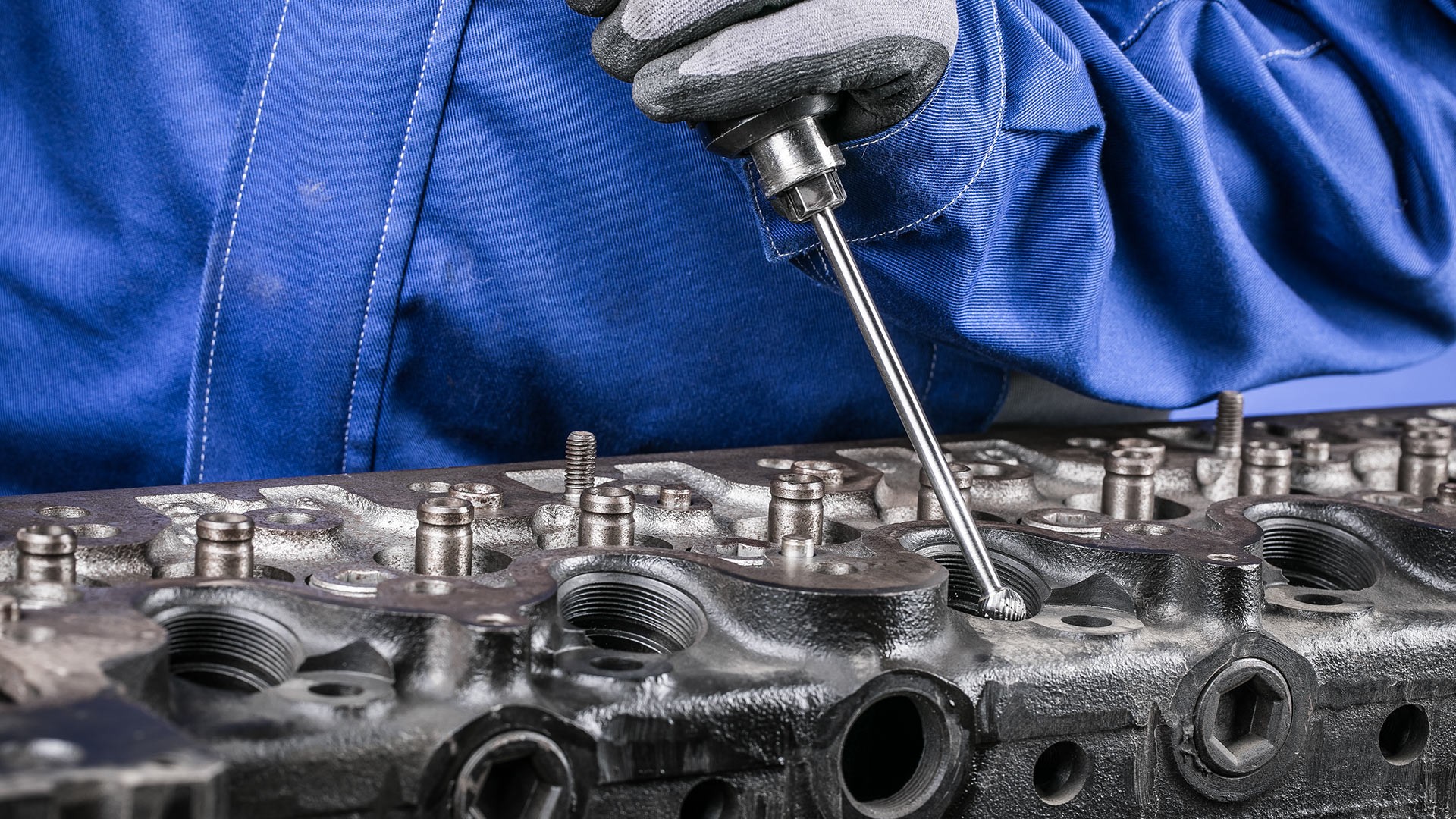
Milling according to DIN: products from PFERD TOOLS for highest quality and maximum reliability
PFERD TOOLS stock removal tools are manufactured in compliance with the highest quality standards. PFERD TOOLS offers an extensive range of TC burrs to DIN 8032. The quality, long service life and excellent stock removal rates of these tools enable users to work more cost-efficiently on different types of materials and to achieve excellent results.
The quality of PFERD TOOLS tools has been certified according to ISO 9001.