How to avoid using burrs incorrectly
Has your burr ever discoloured or its shank broken? Or do sparks occur during milling? PFERD TOOLS will show you how to avoid typical errors when using burrs and offers solutions for your application problem.
Rough running, strong vibrations and parts breaking off the burr
Impacts on the tools and tool chatter lead to premature wear and can cause parts of the cut area to break. It is therefore essential to avoid impact loads when using the tool. Make sure that the surface contact angle/the insertion depth is no more than 1/3 of the circumference of the burr. Otherwise the burr will not operate smoothly and could result in parts breaking off.
Another typical error is not applying a high enough rotational speed when using burrs, e.g. with an electric screwdriver or power drill. Remember: rotational speeds that are suitable for drilling are much too low for milling. This is because when the speed is too low, the tool doesn’t run smoothly. You’ll hear and feel the burr begin to vibrate or even strike the material, which will cause it to wear away more quickly or become damaged. We recommend using the highest rotational speeds possible within the recommended rotational speed and cutting speed ranges.
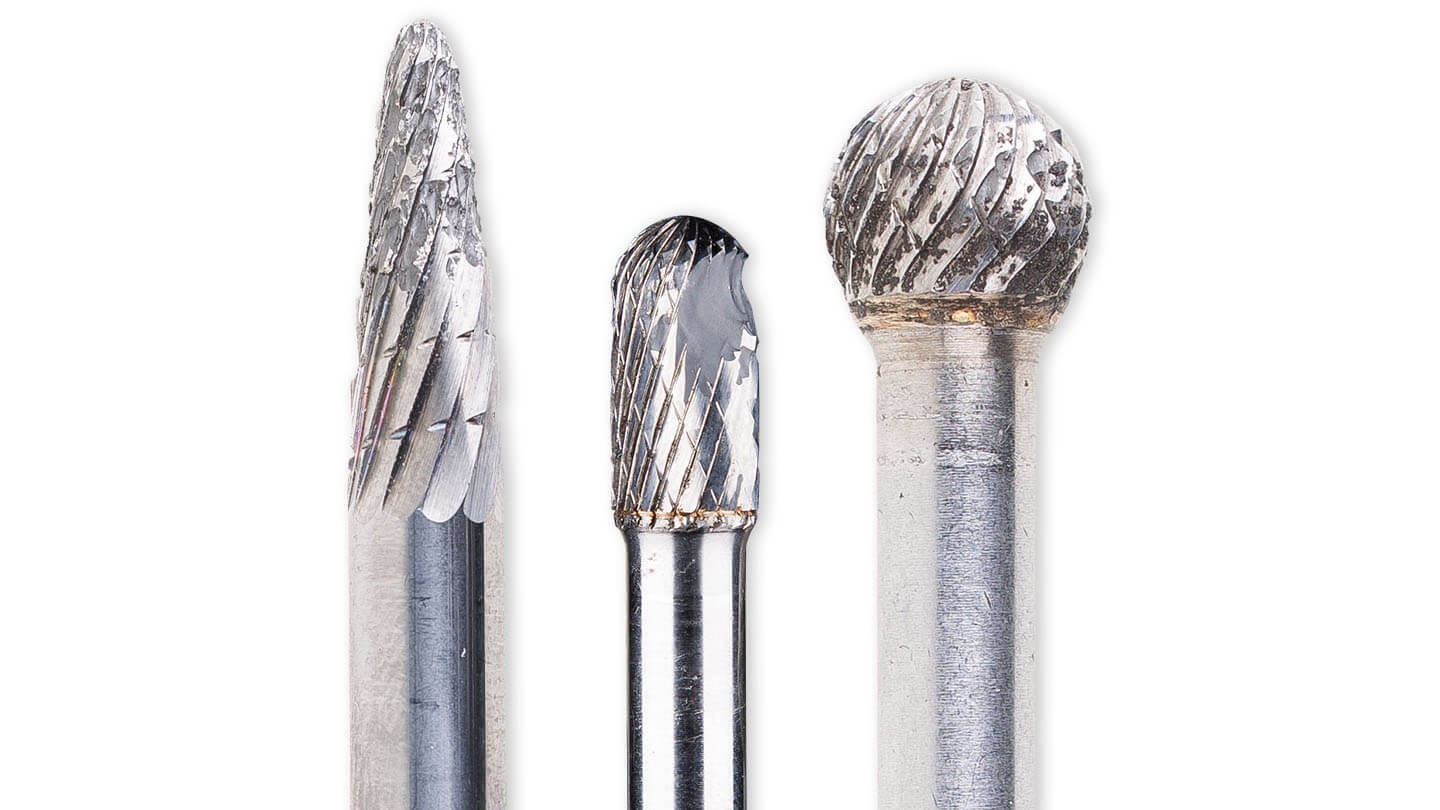
Sparks fly during milling
If you experience flying sparks when using a burr, this is a sign of a specific error during application. One thing that can cause sparks is when the burr is pressed too hard against the workpiece. The solution is to reduce the contact pressure. Another cause of flying sparks is when the rotational speed is too high. You should also make sure that the surface contact angle is no more than 1/3 of the circumference of the burr.
If you have adjusted all the parameters in line with our recommendations for use but the sparks are still occurring, you should check the burr for signs of wear. If you do indeed find signs of wear, use a new burr.
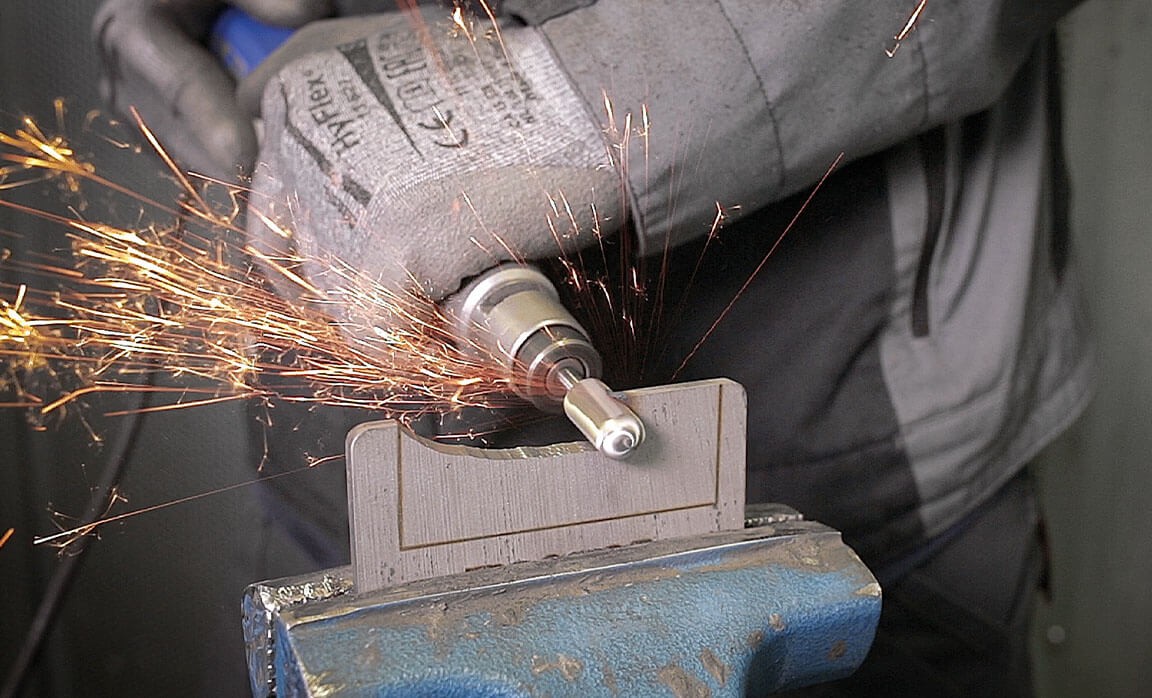
The burr becomes clogged
There are a number of things that can cause a burr to become clogged during application. Remember, the general rule is that, the softer the material you are working on, the rougher the cut of the burr has to be. So the first thing you should do is check whether you are using the right cut for the material. If you are already using the right cut, PFERD TOOLS recommends using tools with a HICOAT coating or using grinding oil.
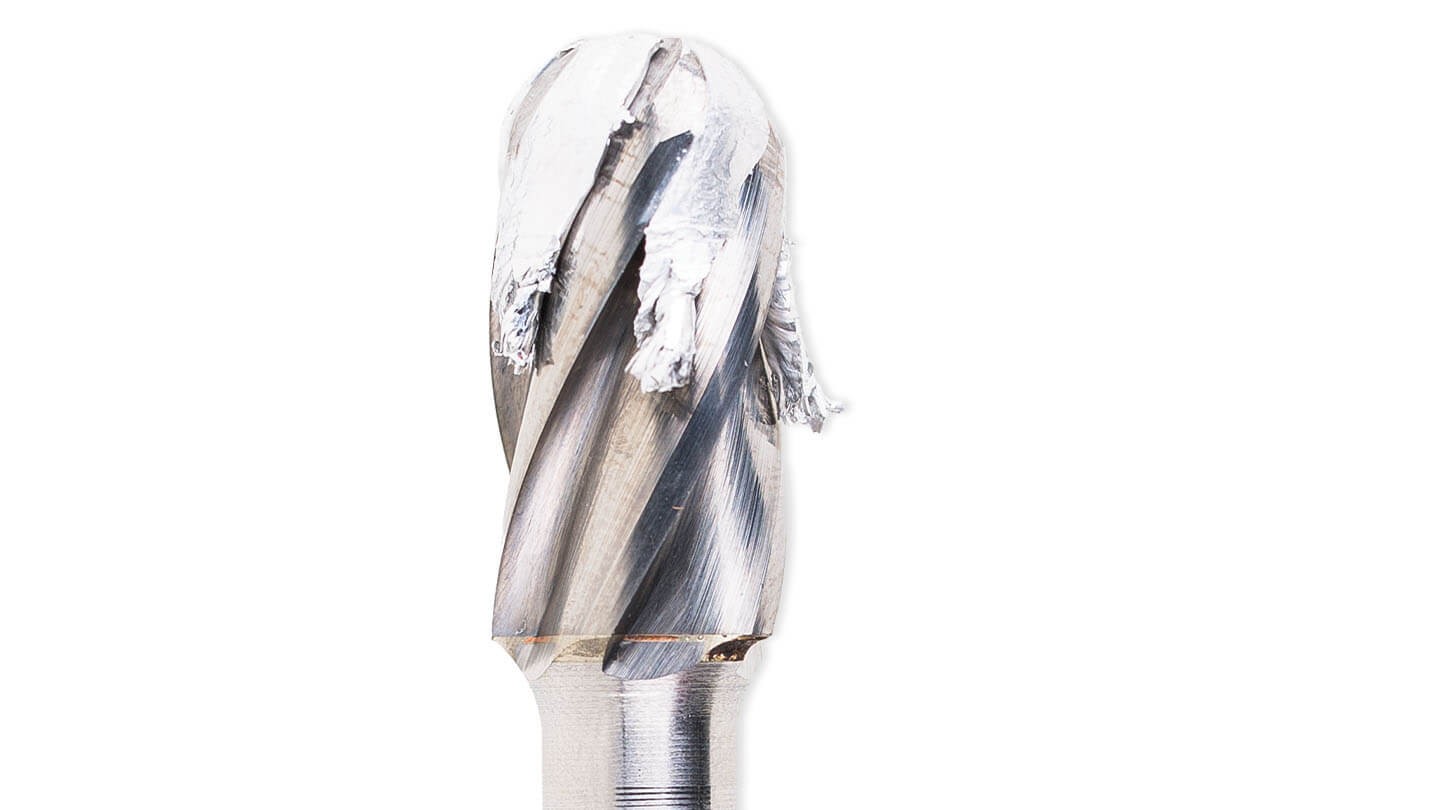
The burr becomes discoloured or the cut area breaks off
If the cut area breaks away from the shank or the part between the cut area and the shank becomes heavily discoloured, you should adjust the rotational speed, contact pressure and surface contact angle. Observe the recommended rotational speeds and reduce the contact pressure and surface contact angle.
Note: When using PFERD TOOLS TC burrs designed for high-performance applications, it is extremely difficult to prevent them from turning blue due to the very high stock removal rate. However, this does not constitute a safety risk.
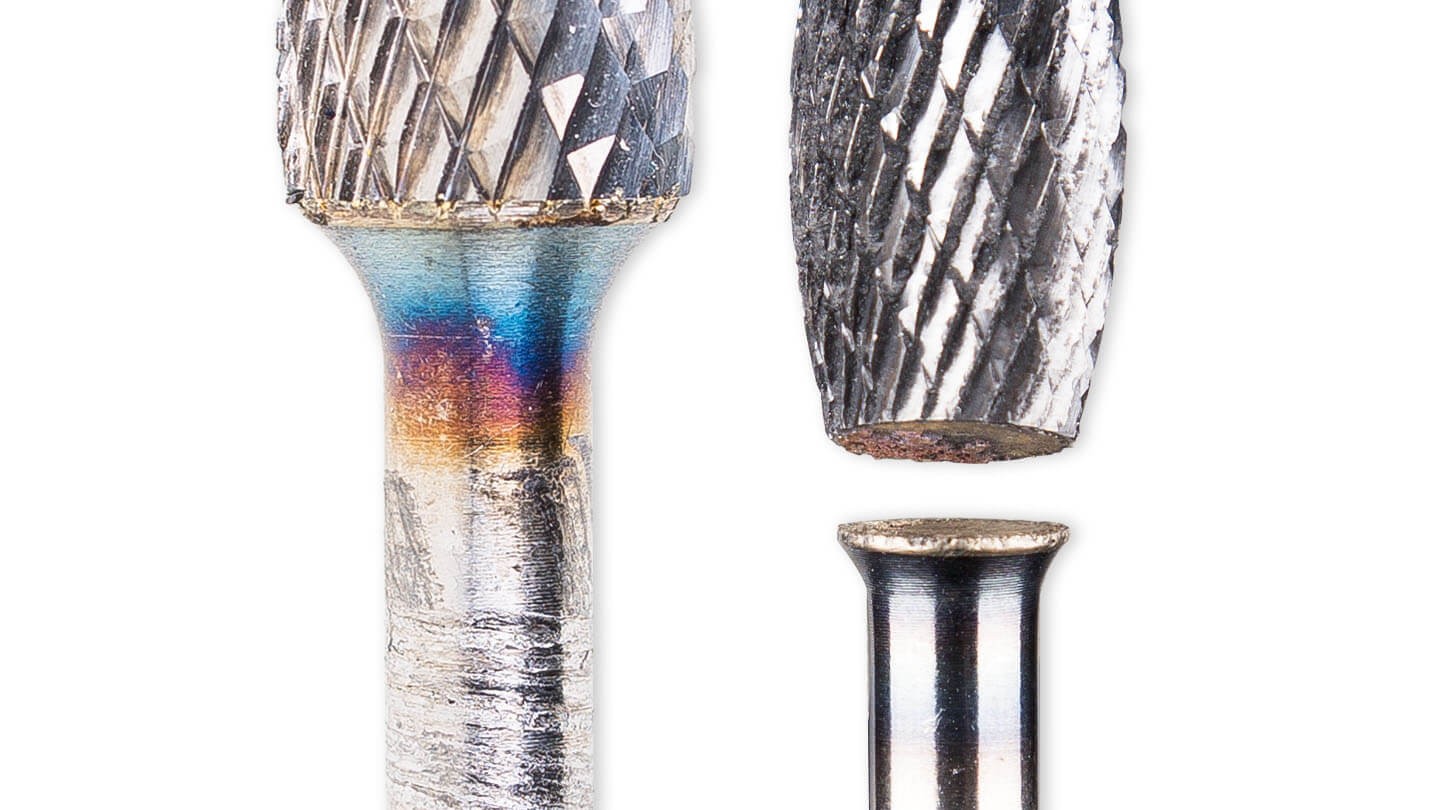
The shank breaks
If the shank of the burr has broken, this can be a sign that the clamping system is damaged. Check whether the clamping system you are using is damaged, and if it is, replace it. You should also make sure that the drives you are using are rigid and as powerful as possible, as this will help to prevent vibrations
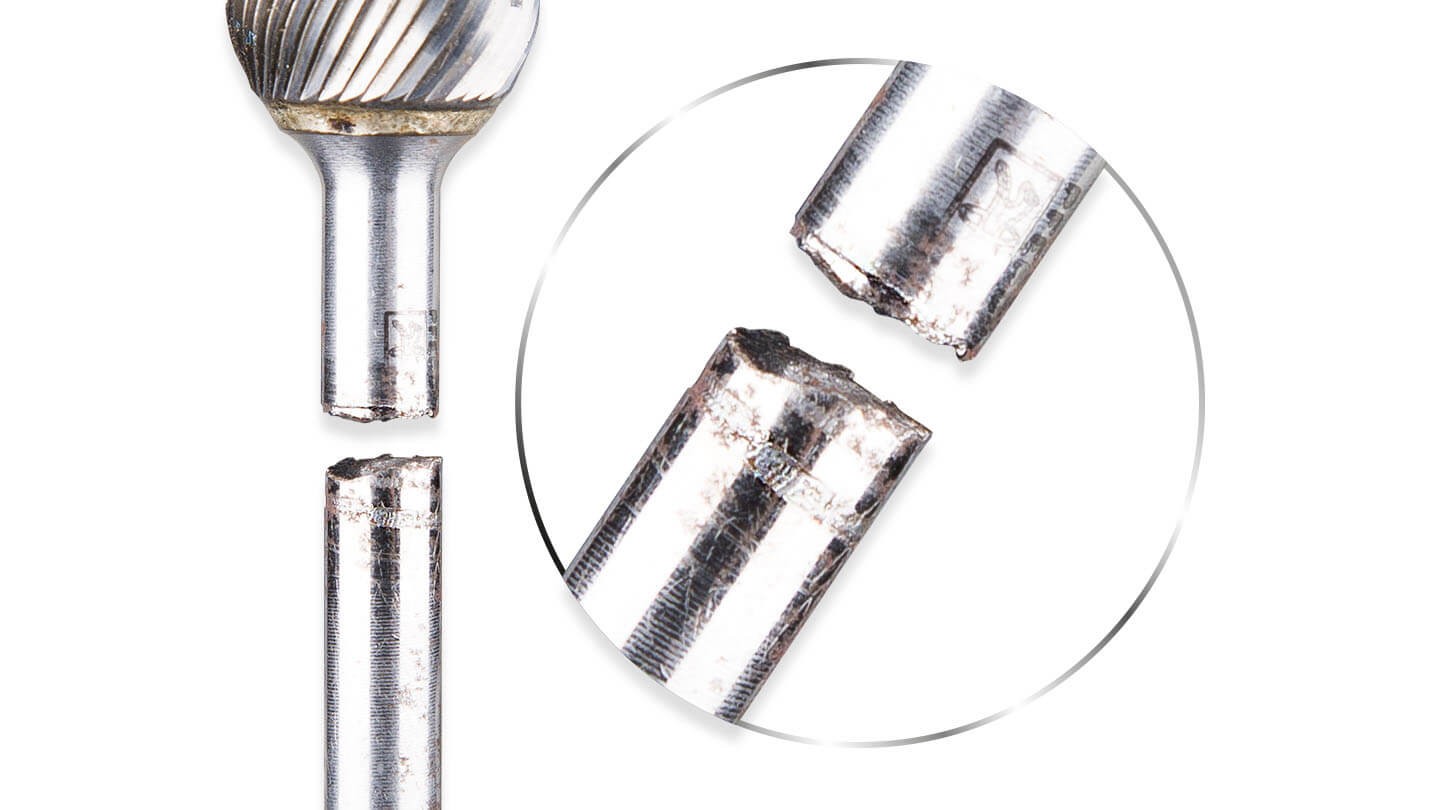
Signs of wear
If, despite using the right milling technology and rotational speed, the burr still doesn’t run smoothly, vibrates a lot or generates more and more sparks, these are signs that the burr is worn. In this case, you should stop using this burr and use a new one instead. Do not use burrs beyond the end of their service life.
Depending on the cut and the dimensions, some tungsten carbide burrs can be resharpened. PFERD TOOLS offers a tungsten carbide burr resharpening service, subject to a minimum resharpening quantity of 25 units (unmixed items). In each case, our production specialists will decide whether resharpening makes sense from an economic point of view and is technically feasible.
Please contact us for further details.